Sand Casting
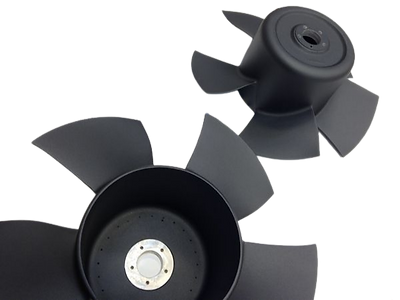
What is Sand Casting?
Sand casting is a metalworking process characterized by using sand as the mold material. Molten metal is poured into the sand mold cavity to produce complex part shapes. Over 60% of all metal castings are produced in sand foundries.
Sand molds are economical and functional for a wide range of metals. A clay bonding agent is mixed with the sand, and the mixture is moistened to create an aggregate suitable for molding. The sand is contained in a system of frames or mold boxes known as a flask. The mold cavities and gate system are created by packing sand around a master pattern, by carving directly into the sand, or by 3D printing or machining.
How Does Sand Casting Work?
Sand casting occurs in six steps:
Place a pattern in sand to create a mold.
Incorporate the pattern and sand in a gating system.
Remove the pattern.
Fill the mold cavity with molten metal.
Allow the metal to cool.
Break away the sand mold and remove the casting.
There are two primary methods of sand casting — green sand and air set:
Green Sand Casting
Green sand castings are made using sand molds formed from wet sand which contains water and clay. The name "green sand" comes from the fact that the sand mold is not set — rather, it is still in the green or uncured state even when metal is poured into the mold. The sand is not green in color, but "green" in the sense that it is used in a wet state (similar to green wood). Sand castings made from coarse green sand impart a rough texture to the surface, and this makes them easy to identify. Castings made from fine green sand can shine as cast but are limited by the depth-to-width ratio of pockets in the pattern.
Air Set Sand Casting
The air set method uses dry sand bonded with materials other than clay. The use of a fast curing adhesive is referred to as no-bake sand casting because the molding sand sets at room temperature. Air set molds can produce castings with smoother surfaces than coarse green sand. This method is primarily chosen when deep, narrow pockets in the pattern are necessary, due to the expense of the plastic used in the process. Air-set castings can typically be easily identified by the burnt color on the surface. The castings are typically shot blasted to remove that burnt color. Surfaces can also be later ground and polished, with post-molding residue removed via grinding or shot blasting.


Advantages of Sand Casting
Sand casting offers many advantages, some of which include:
Viability in nearly any ferrous or non-ferrous alloy
Low tooling cost relative to other casting processes
Versatility of part size, weight, and shape — from ounces to 200 tons
No quantity restrictions — prototyping to mass production
Shorter time to market than many other casting processes
Sand Casting Materials
Sand casting can be used with a wide range of metal alloys. Most commonly:
Aluminum
Zinc
Steel
Bronze
Brass
Magnesium
Iron
Various pot metal alloys, which often include lead, tin, and Zinc
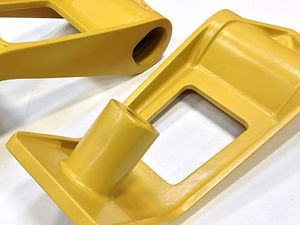
Sand Casting Applications
Sand casting is used in a wide range of industries and products. Some examples include:
Energy: Pump and valve components, dewatering grates, petrochemical fittings, hydropower wicket gates, tube sheets
Industrial: Stage bases, scanning components, carriages, forks, flange frames, hinges, stiffening covers, adapter housings, supports, chassis
Medical: Cart bases, robotic arms/knuckles, display housings, equipment enclosures, handles, chair components, internal structural components, foot pedals
Technology: Integrated heatsinks, optic trays, networking boxes, ruggedized hand-held devices, USB components, LiDAR
Transportation: Agricultural equipment, autonomous farming devices, search and rescue GPS equipment, self-driving trucks