Reaction Injection Molding
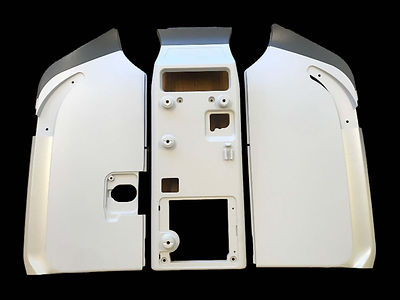
What is Reaction Injection Molding?
Reaction Injection Molding (RIM) is a low-pressure, low-temperature process used to produce complex plastic parts. RIM is similar to injection molding, except that thermosetting polymers are used — which requires a curing reaction to occur within the mold. RIM is often utilized for the molding of strong, lightweight parts that are easily painted.
RIM material is typically a two-component system of Polyol and Isocyanate liquids that are mixed at high pressure, then metered into a closed tool at low pressure. The material then expands to fill the tool and ejects in about 5 minutes. Rigid RIM materials often come with a UL94V-0 rating for flammability.
How Does Reaction Injection Molding Work?
Reaction Injection Molding begins with two low-viscosity polymer liquids — Polyol and Isocyanate. The polymers are stored in tanks and dispensed by high-pressure industrial pumps. The two-component RIM material circulates in a continuous loop between the storage tanks and a multi-stream mix head.
RIM material systems expand and thicken through a variety of chemical reactions. After the polymers have been injected into the heated mold, they gradually solidify. Through the RIM design process, different raw materials and molding techniques can be selected to deliver customized part weight, strength, density, and hardness. The resulting polyurethane parts can have lighter weight and more intricate features than shapes created by traditional injection molding.
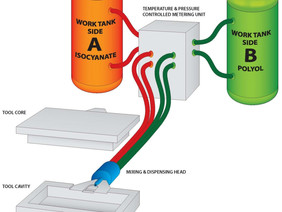


Advantages of Reaction Injection Molding
RIM allows for many distinct advantages, some of which include:
Large parts - The properties of the liquid polyurethane components enable them to fill molds for very large parts.
Encapsulation of inserts - Inserts of many types can be placed into a mold prior to injection of the RIM material. The RIM material can also encapsulate many inserts during molding.
Thick and thin walls in the same part - The RIM process offers you the flexibility to design parts with significant wall thickness variations.
Class A surfaces - The surface finish of parts molded with the RIM process allows manufacturers to produce Class A painted parts.
Low cost tooling - The low injection pressures of the RIM process allow for tooling to be manufactured quicker, and at lower cost, than tools used in injection molding or structural foam molding.
Reaction Injection Molding Materials
The most common plastics used in RIM include:
Rigid Polyurethanes
Elastomeric Polyurethanes
Polyamides
Fiber Composites
Structural Foams
Flexible Foams
Dicyclopentadiene (DCPD)

Reaction Injection Molding Applications
Reaction Injection Molding (RIM) is used in a wide range of industries and products. Some examples include:
Defense: Airport luggage scanners, security screening equipment, EMI/RFI shielded enclosures
Energy: Metering equipment, smart grid components, fluid handling equipment
Industrial: Containers, irrigation system enclosures, fluid handling systems, carts, kiosks
Medical: Medical cart skins, diagnostic laboratory equipment enclosures, medical equipment panels, equipment vents, drug delivery devices, respiratory equipment, surgical and medical robotics, imaging components, dental equipment, biotech devices, life sciences instruments, analytical instrument enclosures, patient treatment chairs
Technology: Electronic device housings, electronic storage enclosures, vented panels, robotics, touch screen enclosures / bezels